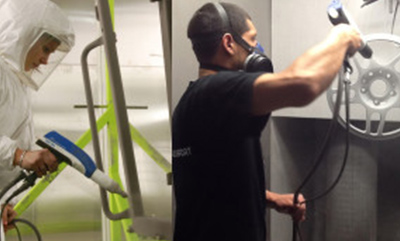
Powder Coating Tips in Hot, Humid Weather
Low flow powder coating solutions for class A finish
Despite the important role that heat plays in the formation of a durable coating, hot humid weather can negatively impact results of the powder coating process.
Many of us have experienced changes or difficulties coating in the hot, humid summer months. In fact, our team recently responded to a question from a powder coater in Vietnam having issues with coating in the extreme humidity, and we thought we'd share the advice we gave them! If you live in this type of climate condition, here are some tips for how to address this issue in your powder coating facility.
How Do Heat & Humidity Affect Power Coatings?
Clumping
High humidity levels can cause the powder material to absorb moisture and clump together, making it harder to fluidize and spray evenly. Moisture can also interfere with the electrostatic charge and reduce the adhesion of the powder to the surface. Additionally, excess humidity can cause discoloration or staining of the powder coat if it is trapped inside the coating before curing.
Clogging Equipment
High temperatures increase the risk of impact fusion, which is when the powder particles melt and stick together inside the gun or along the passageways. This melted coating can reduce the powder flow and charge, resulting in poor coverage and quality. You may also be experiencing increased gun/pump/injector maintenance issues and surging. Corona charging applicators are affected by heat & humidity as well, but Tribo is more susceptible to environment and powder formulation.
With high humidity and increased temps, your compressed air dryers, oil removal, and particulate filters will get a workout. Make sure all drains and dryers are operating properly. The compressed air must be clean, dry, and oil aerosol free.
Curing
Hot weather can also increase the curing time and temperature of the powder, which can affect the gloss, color, and other properties of the final coating. High temperatures can also cause oxidation and degradation of the powder, reducing its shelf life and quality. Hot weather increases the risk of corrosion, especially in coastal environments where salt is present.
Hot Humid Weather & UV Curable Powder Coatings
UV curable powder coatings are a type of coating that can be cured by exposure to ultraviolet (UV) light. Unlike conventional powder coatings, which require high temperatures and long baking times, UV curable powder coatings can be cured in a matter of seconds at room temperature. This makes them more energy-efficient, environmentally friendly, and suitable for heat-sensitive substrates.
UV curable powder coatings are impacted by hot weather and humidity in different ways. Hot weather can increase the viscosity of the coating, making it harder to apply and more prone to sagging or dripping. Humidity can affect the curing process, as moisture can interfere with the photoinitiation reaction and reduce the crosslinking density. To prevent these problems, UV curable powder coatings should be stored and applied in cool and dry conditions, and cured as soon as possible after application.
Best Conditions for Applying Powder Coating
It is important to control the temperature and humidity of the powder storage and application areas. The recommended conditions are 70-80°F (21-27°C) and 55% relative humidity. These conditions can help prevent moisture absorption in most powder coatings.
Remember, powder is hygroscopic and will absorb all the moisture you allow. Humidity above the recommended 55% will adversely affect the ability to charge powder and the charged particles' ability to retain the charge. This also affects the transfer efficiency and uniformity of the coating.
How to Address Problems with Powder Coatings
The curing schedule for each type of powder will vary, but be aware low temperature cure powders tend to have less color stability. It's important to select the right powder formula, primer, and topcoat for your specific environment and application.
- Some powder formulas, such as FEVE resin-based ones, have more weather resistance than traditional ones.
- Some primers, such as zinc-rich primers, can protect against moisture penetration and corrosion.
- Some topcoats, such as polyester, acrylic or fluoropolymer, provide extra sunlight protection.
There are no effective post-blend powder additives for high humidity conditions. However, there are known post-blend additives the powder manufacturer adds during production to enhance powders ability to tribo-charge. Did you recently change batches of powder? You might want to check with your powder supplier to assure something didn’t change on the batch ticket. Another question for you to consider: Do you have excellent earth ground? Do you know where your “earth ground” is located? Can you identify all contact points and know resistance values?”
For more information, check with CCAI (Chemical Coaters Association) & PCI (Powder Coating Institute) handbooks or any number of other references for the powder coating industry.
For The Best Powder Coating Equipment, Choose Parker Ionics
Parker Ionics supplies powder coating guns, nozzles, hoppers, booths, and other powder coating accessories. We also provide maintenance, training services, audits and testing, and powder coating parts and repairs. It's our goal to ensure you get the powder coating solutions you need to grow your business.
We hope you've benefitted from these powder coating tips in hot humid weather. For more information, contact us or reach out directly to Parker Ionics Regional Sales Manager Mike Nugent at mnugent@parkerionics.com.